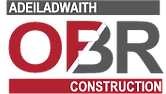
Penmon Ynys Mon
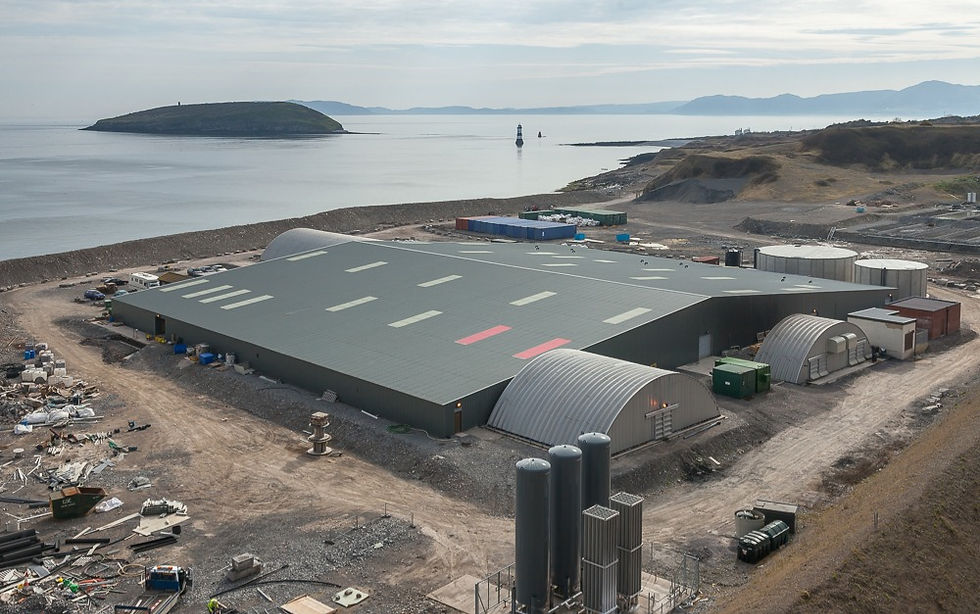


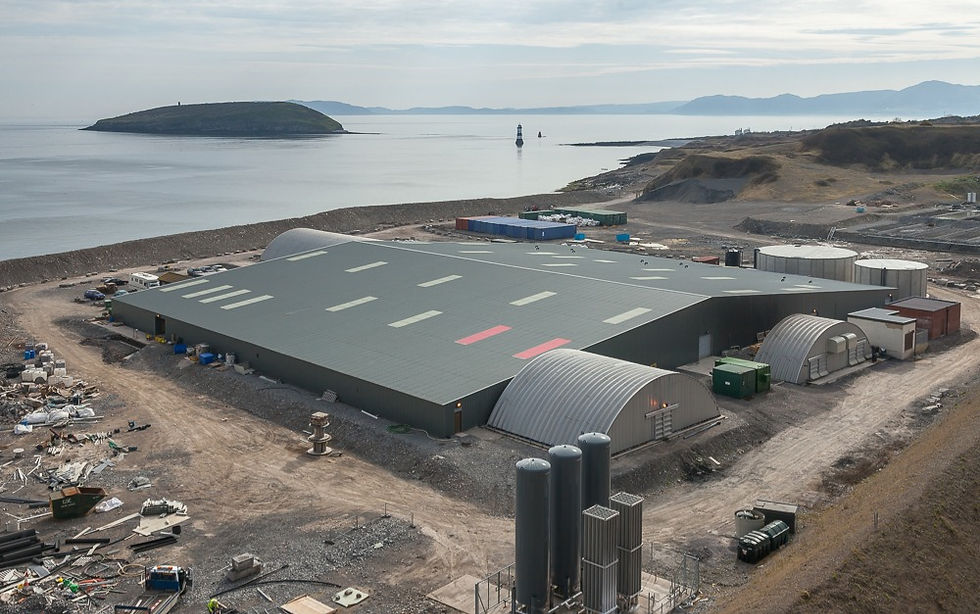
fish farm
Development
Phase 1
The project is split into two main areas of work. The refurbishment work of the current fish farm facilities and construction of a new steel frame building to house additional tanks.
The refurbishment of the current tank area included:
-
Demolition of old tanks
-
Excavation to deepen and widen the tanks
-
Extensive structural reinforced concrete walls and slabs to form new tanks. The tanks measured 5m deep and 25m diameter.
-
New drainage to service the new tank capacities
-
Sika coatings to concrete finishes to ensure correct ph levels in the water tanks
-
Service trenches
The construction of the new building included:
-
Excavation, foundations and floor slabs.
-
Steel Frame structure
-
Kingspan panel wall and roof system
-
Formwork and cast new breeding tanks
-
New services inc water mains and sea water, 3 phase electricity, security system and telecommunication
-
Drainage and catchpits.
The project presented two critical issues that we had to work around for a successful deliver.
-
Location
Penmon on Anglesey is a remote location and the fish farm was off any service road. The access was tight and rocky, and deliveries were not possible on large articulated vehicles. By engaging with our local supply chain and coming up with simple resolutions to these problems, we avoided any increase in time and cost to the project. It also made the concrete pour challenging as the distance from the plant minimized our time before spoil on site. We had to make sure all operatives and work was ready for each pour and communicated with the plant to say when to start sending the next delivery. -
Environmental Impact
This was a challenge on two fronts. 1st being the close proximity of the work to the sea and the 2nd being the current operation of the farm and future use of the newly constructed tanks.
As we were undertaking extensive concreting close to the sea, we had to take extra steps to ensure none of the chemicals entered the water system. This could happen through drainage, groundwater pollution or during pour washout. Temporary structures were constructed around our pour areas to catch any chemicals, neutralise and dispose of safely. Lorries were washed before leaving site with all water pumped into treatment tanks.
The end use of the tanks was also critical to account for, as any chemical residue or dirt in the system or tanks could potentially cause a large loss of stock and money to the client. By adhering to strict protocols installed by the client we ensured that all casting was done in line with their worldwide QA system, and samples were taken throughout the process of all material used and water residue and sent to their Laboratory to analysis. Through systematic cataloging of samples, we would easily locate and rectify any negative result. None were found during the works.
​