Project: Hafod Eryri Roof Renewal
Location: Summit of Wyddfa (Snowdon Summit)
Client: Parc Cenedlaethol Eryri – Eryri National Park Authority
Approx. Value: £580,000
Timeline: 12 months
Contract: JCT Design and Build
OBR were awarded the project of refurbishing the buried flat roof of the summit café of yr Wyddfa, formally known as Snowdon. With an elevation of 1,085m and only accessed via the train, this was one of the most unique and challenging projects we have completed. The brief was to expose the buried flat roof that was covered by over 500mm of stone ballast that is heavily trafficked by the visitors of the summit, remove the failed EPDM membrane and design and install a new roof system. During the tender process, OBR worked closely with Sika to provide an outline specification and scope that would allow us to offer a robust and durable solution to the roof that provided the weather proofing to the building plant room and café area. With our experience of construction and roofing, we also carefully considered the build ability of the solution and methodologies to ensure maximum safety to our customers, operatives and the building structure. After careful consideration we decided on the Sika bitumen membrane solution, opting for the 25-year SikaShield torch on felt system.
The project was split over two phases, the first starting in September 2023 so undertake initial trial and investigation works to refine the design and install a trial area to ensure the system and methodology would work in the hostile environment. During this process, we initially engaged with a structural engineering team to review the loading capacity of the roof as we needed to move a large quantity of stone ballast around the roof with excavators and plant. Following the results of this calculation, we had to change our methodology to minimise the loading on each section of the roof to stay within the loading capacity of the concrete structural beams. This increased the project duration by only allowing 30m2 roof areas to be exposed at once, but minimised the risk of structural damage and leaks into the live building.
The next challenge was to establish a site on a remote mountain summit which was surrounded by an SSSI (Site of significant Scientific Interest). Our site hoarding, fencing would need to be able to stand up to 100mph winds without damage or falling, causing a serious injury risk to anyone on the summit. The perimeter fencing was ballasted using 200kg feet each panel, with cross bracing and additional brackets. The fence was continuously review and inspected on a weekly check and following any severe weather event, and panels were replaced as required to maintain integrity of the site.
Access to the summit was by train each morning that the café staff travelled up on. From the platform, scaffolding and a hacki staircase was installed to allow contractors to access the roof area without disruption to the café which is the main route from the platform to the summit. The scaffolding contractor had to design the system and undertake pull out tests of the stone cladded wall to ensure that their structure to withstand the wind at the summit.
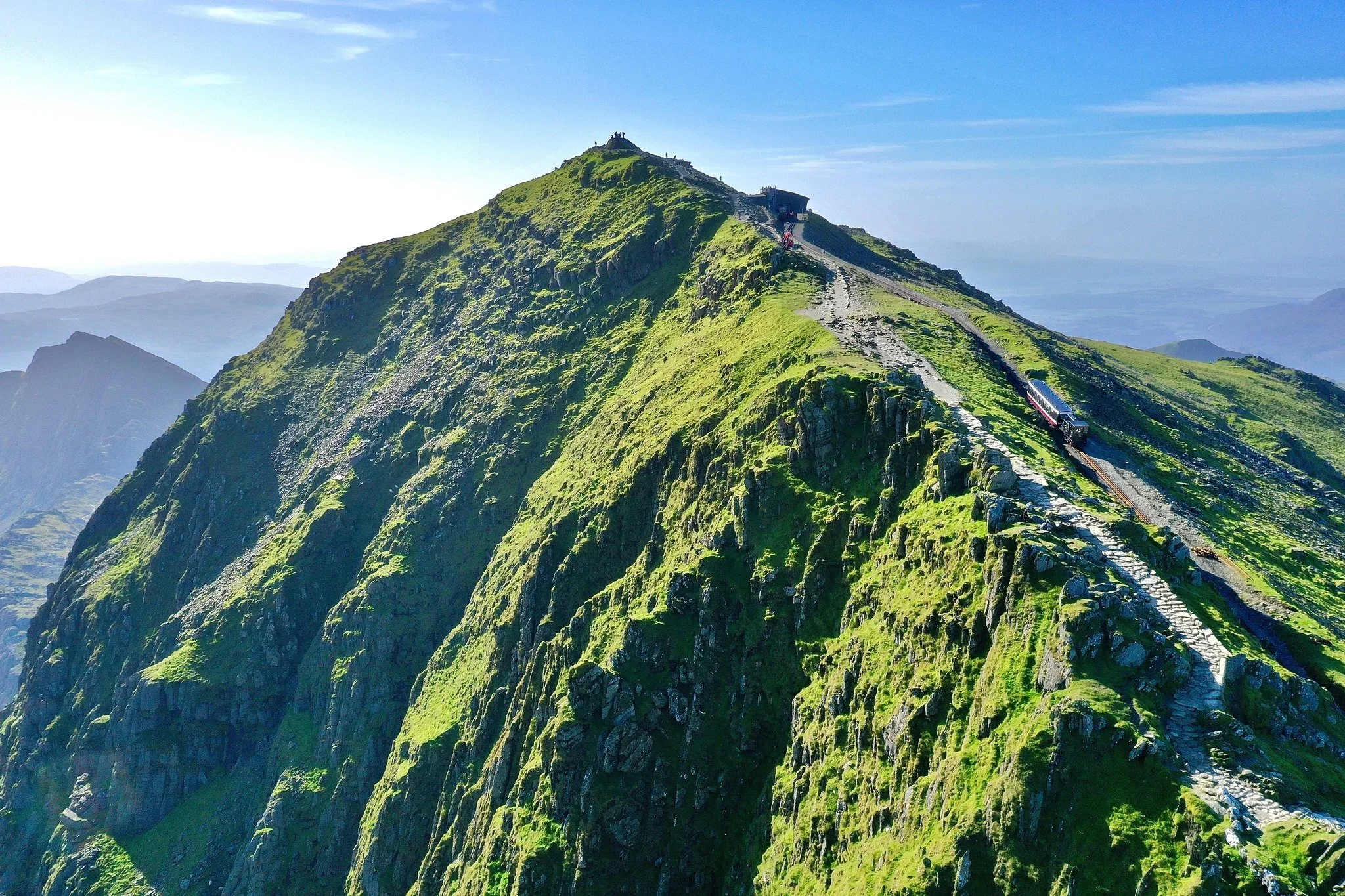
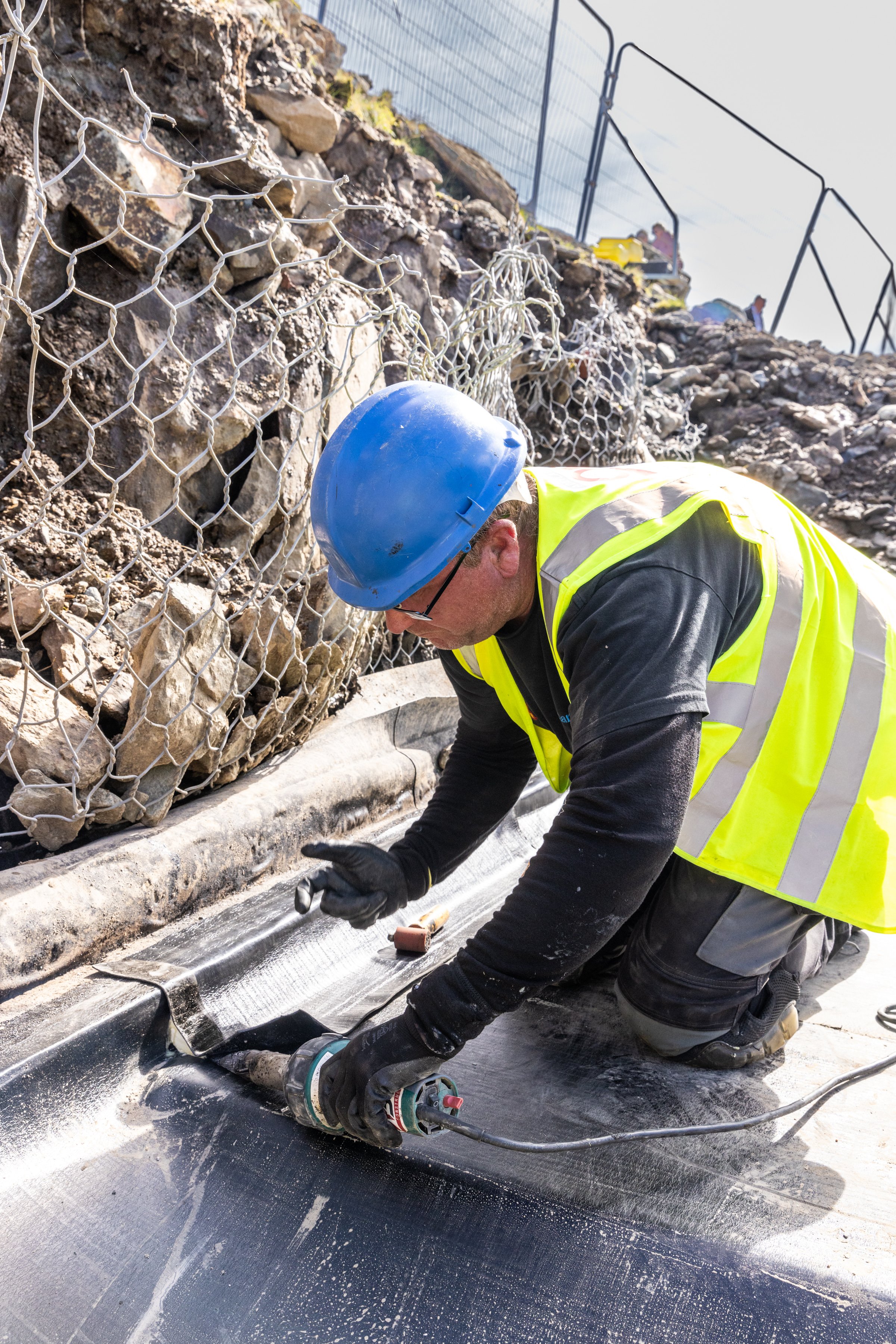
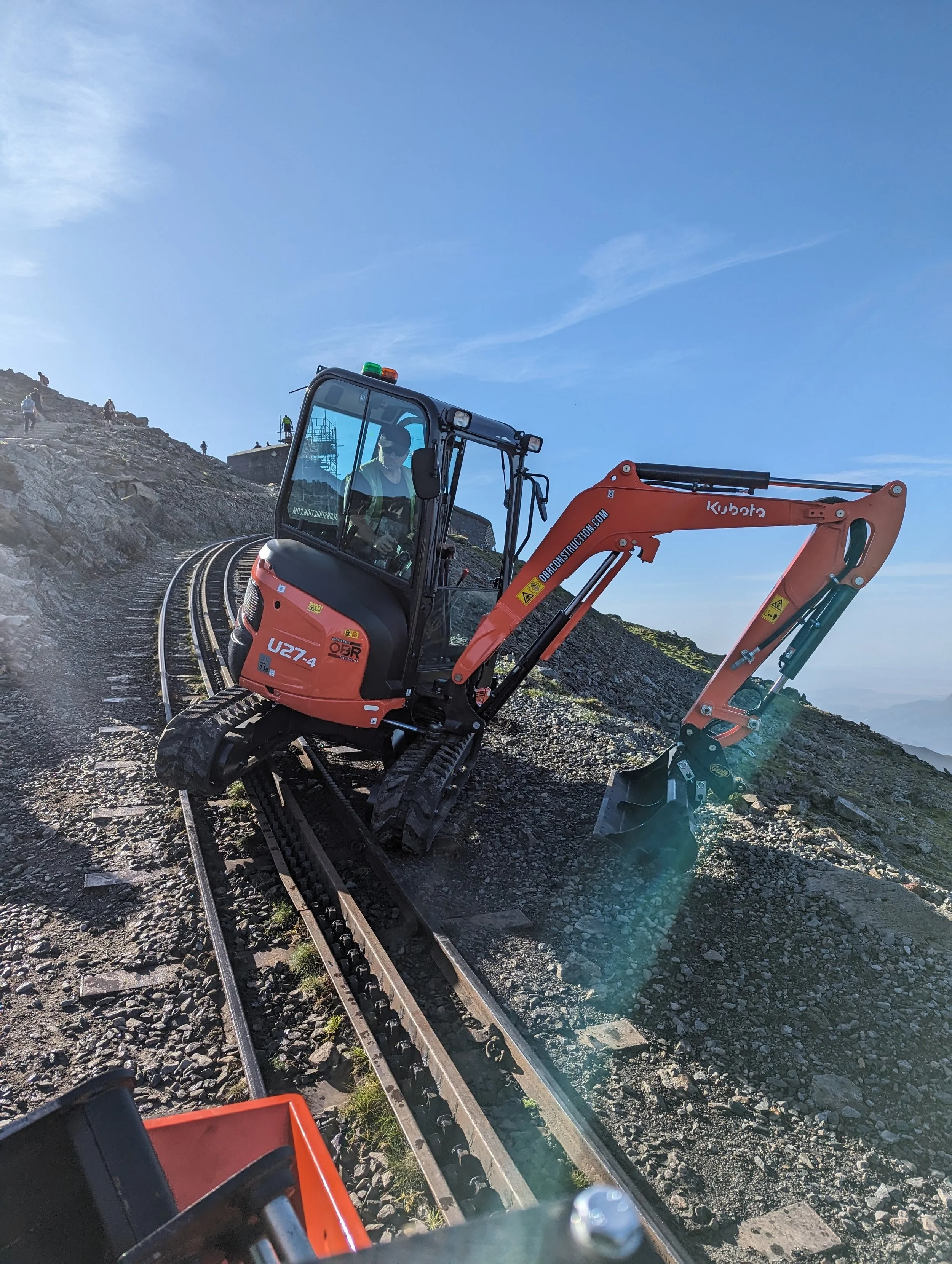

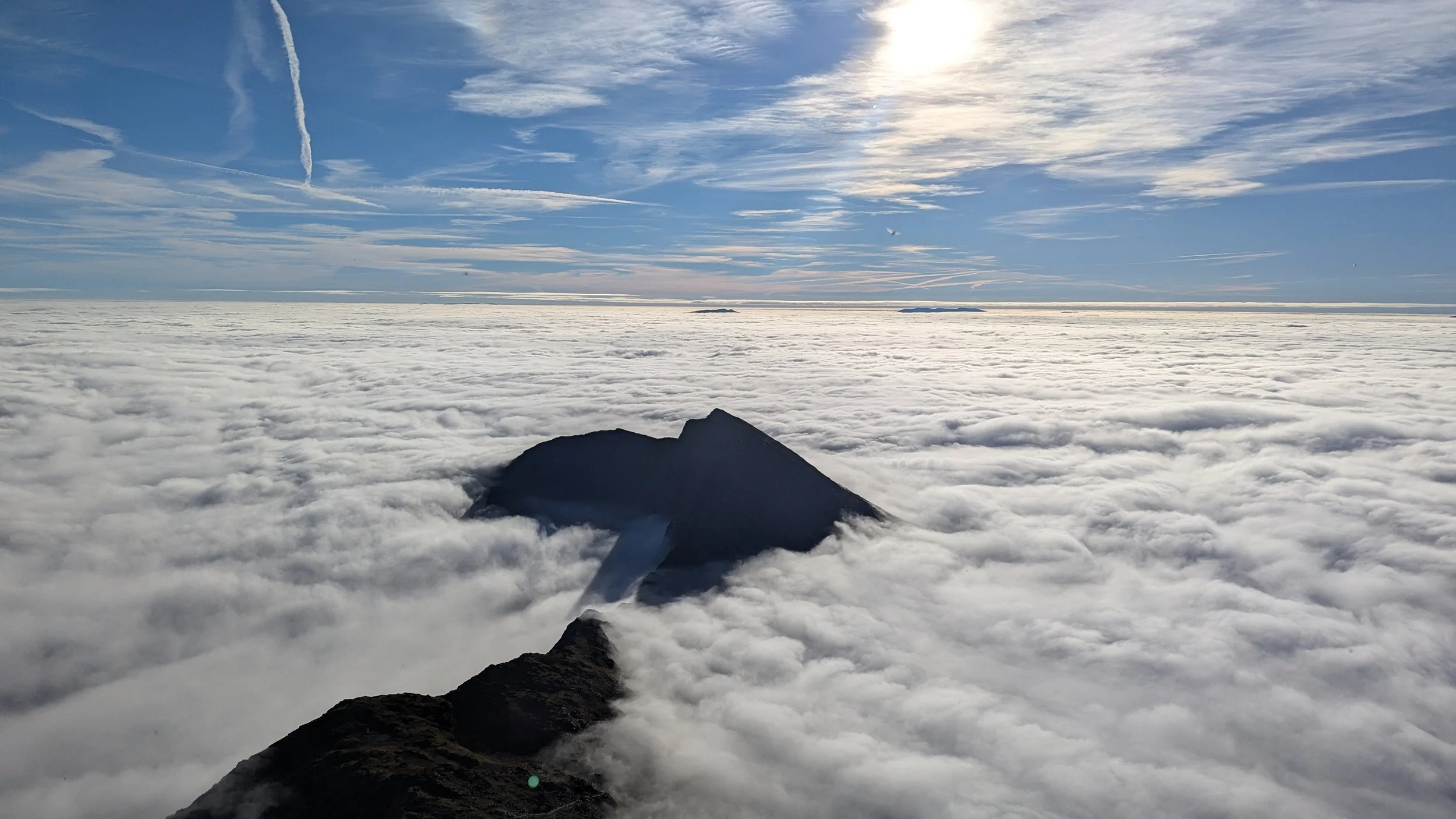
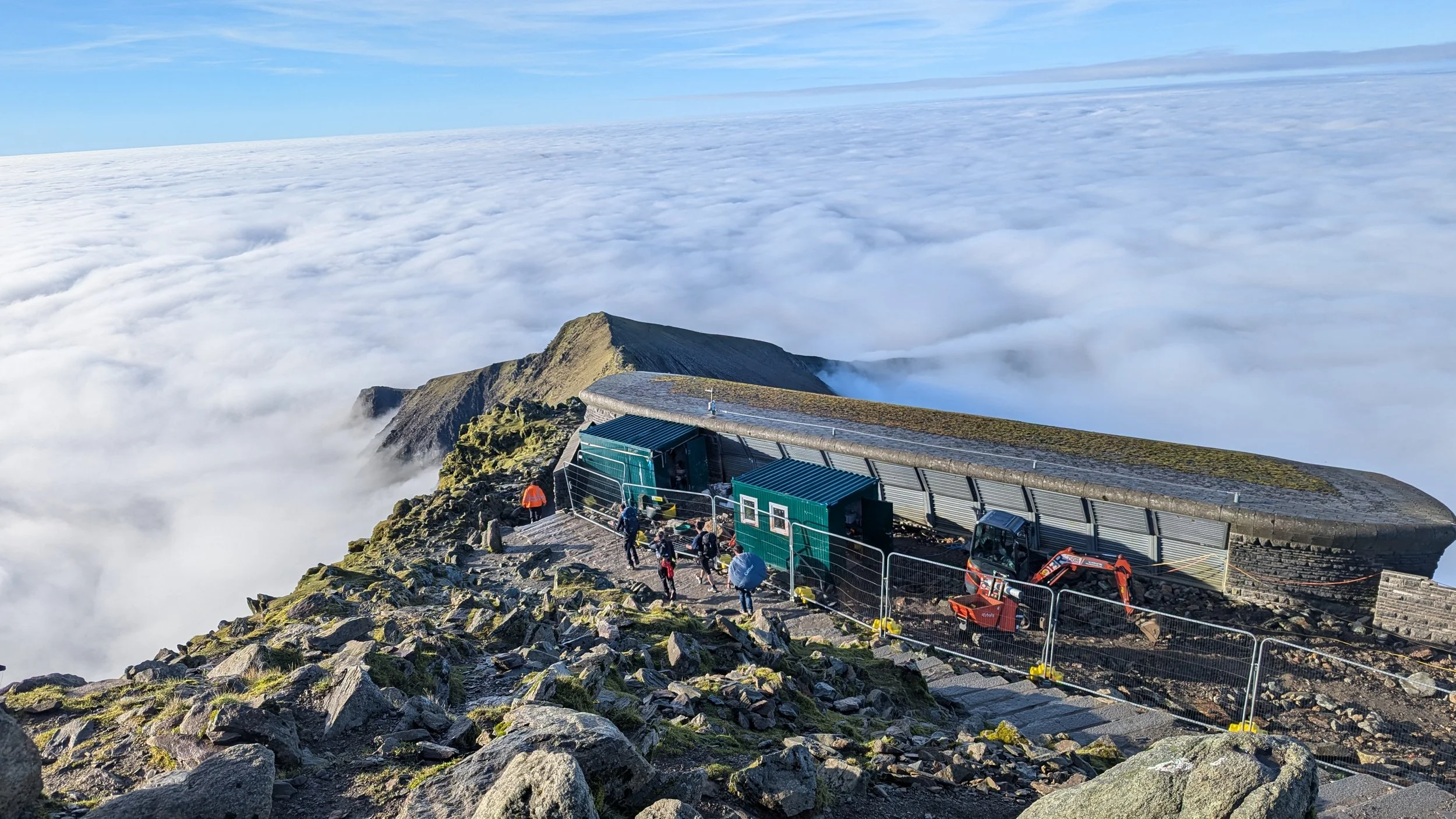
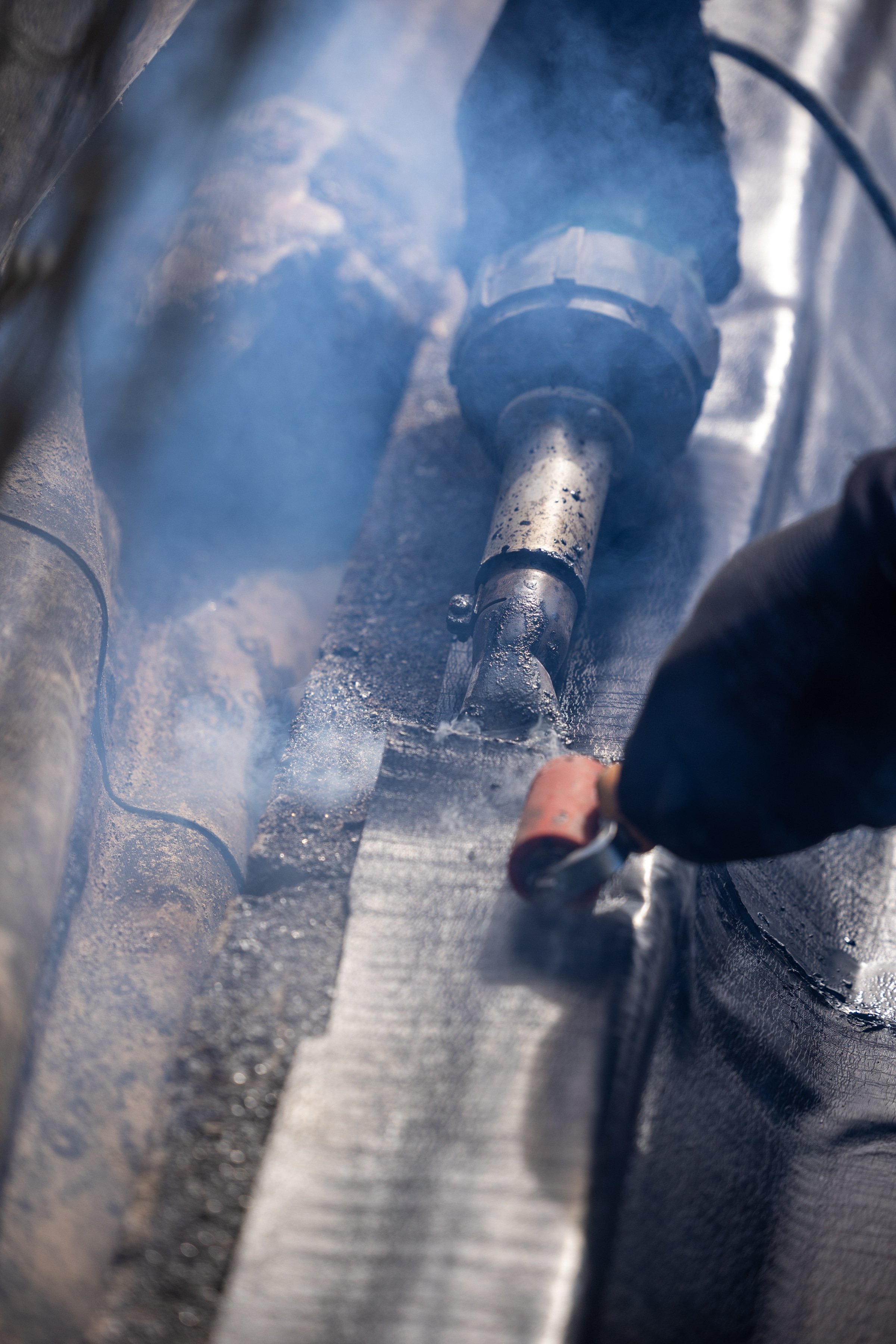
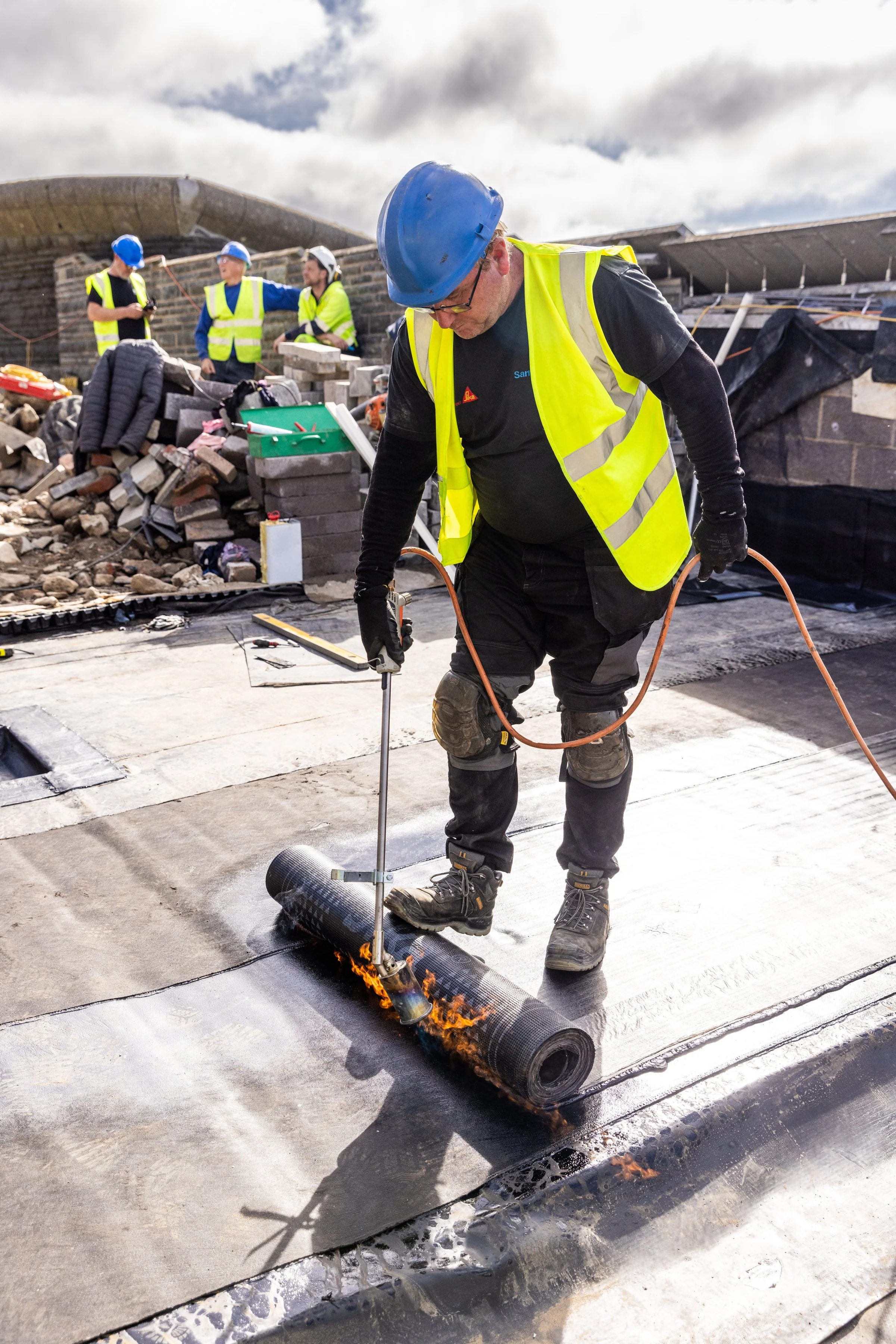
With the site establish, the next challenge was transporting the 3t excavator and 1t dumper to the summit. The morning train had a flat bed that we could load the plant onto at the base of the mountain, but could only transport them 90% of the way to the summit. The remaining 10% we had to unload the tracked plant off the flat bed with ramps and track up the steep mountain to the summit. This was risk assessed and planned by our in-house health and safety manager, and a team of 10 experienced operatives were tasked with the tasked with the move. We used over 100 sandbags to place on the mountain to even out the terrain, provide traction and protect the mountain for the damage of the tracks. We also had two people ensuing the public were controlled and diverted away from the high risk work area. Both excavator and dumper was successfully delivered up and down the mountain without incident. With the plant on the summit, we were now able to lift two flat pack containers as storage and welfare to the site. These were anchored down to the roof with shot fired fixings into the concrete structural frame. These containers provided shelter and welfare for the site team and storage for all the material required for the days work and tools on the summit. An 11KvA generator was also transported to offer 110v and 240v power at the workface.
Now work could begin, we exposed the first 10m2 of the roof to investigate the true build-up of the roof. What had been installed was a EPDM membrane adhered directly to the concrete beam and block infill, filer fleece layer, inverted roof XPS insulation and finally 100-250mm of screed laid to falls. We found many issues that were causing water ingress into the building, including failed welded joint between the EPDM membrane, loose upstand details, punctured membrane at change in height or upstands. Shrinkage of the membrane cause the EPDM to tent between detail, insufficient upstand height, no cavity trays within the upstand walls.
Our conclusion was that although issues were present within the main area membrane, the main issue was a badly designed upstand and structural parapet wall. As part of our project we decided to remove the outer layer of the wall and dress our membrane up to the top of the parapet wall. This was 1.5m high, but with snow drift reaching this height during the winter months, it was imperative to ensure a robust solution. We also installed cavity trays and weep holes throughout the new outer skin of the parapet, that would catch and discard any water ingress into the wall. A continuous problem the client have on the summit is the stone cladding points failing each winter, with the mortar beds blowing and leaving big holes for driving rain to enter the structural wall. By laying our membrane up to the capping height of the parapet, we negated this issue.
The roof area was designed as a warm roof to allow installation of a tapered insulation board system to encourage water to fall to the internal gutter system and the 6 outlets throughout the roof.
To the end of the first phase, we now had a clear picture of what was required to complete the work and the scope. We has also experienced the brutality of the weather on the summit, with November brining in 80-100mph winds, constant rain and freezing conditions.
Phase two started May 2024 and the site was re-established, and work could start in earnest. Working in the 30m2 sections, we exposed the roof be moving the ballast and spreading among the rest of the 350m2 roof to equally distribute the load, we demolished the screed and removed the insulation and EPDM membrane. All waste and surplus material was transported down to the mountain base by tippable skips installed onto the flat bed of the train. Telehandlers would unload the material down in Llanberis and segregate the waste into the appropriate waste streams. We managed to reduce our waste by donating the insulation to a local scheme that enquired about its final destination. At the summit, the first layer was torch applied to the concrete structure to ensure the initial waterproofing layer was on as quickly as possible. The temporary joint between the new felt membrane and old EPDM was sealed using a self adhesive strip and Sika Liquid applied membrane. As one area was completed, the ballast was moved from the next 30m2 area back onto the newly roof area and the next section could start, repeating the same process. The stonemasons and bricklayers worked tirelessly taking down and rebuilding the parapet wall, allowing the more weather dependent roofing works to progress any time the weather permitted.
We had originally projected the programme completion on June 2024, but due to adverse weather this was pushed all the way to end of September 2024. The train was unable to reach the summit in winds exceeding 50mph, and the train operators later confirmed that 2024 was the worst summer on their record, with the most cancellations in their business history. But thanks to our dedicated project team and local operatives who took great pride and pleasure in working on the iconic Welsh mountain, we completed the work with 2 weeks remaining on the season and avoided having to return to the summit in 2025 to complete the work.
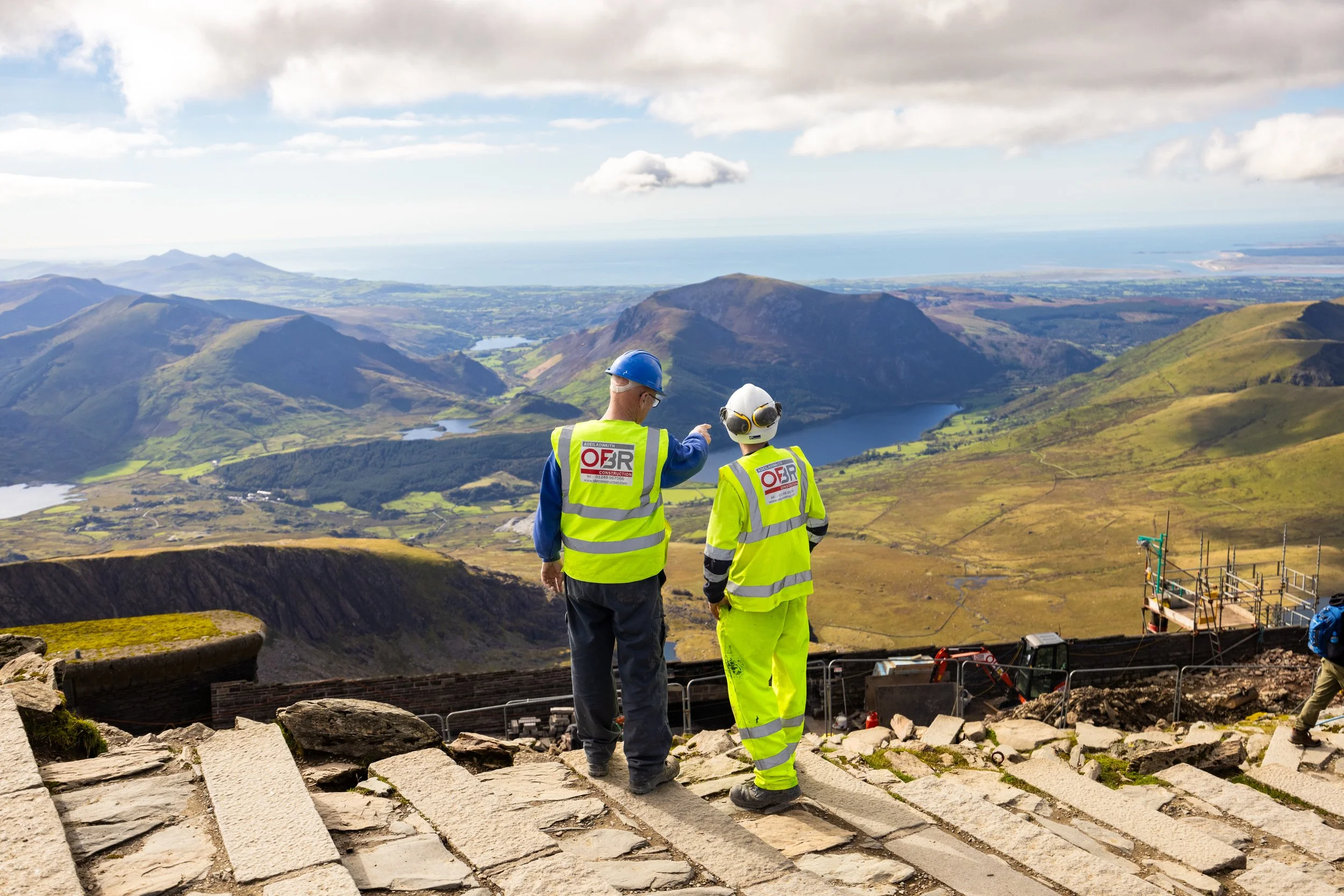